Becoming a Safety Manager: Pursue Your Passion with a Career in Occupational Safety
Explore what it takes to become a safety manager, including key responsibilities, qualifications, and career outlook.
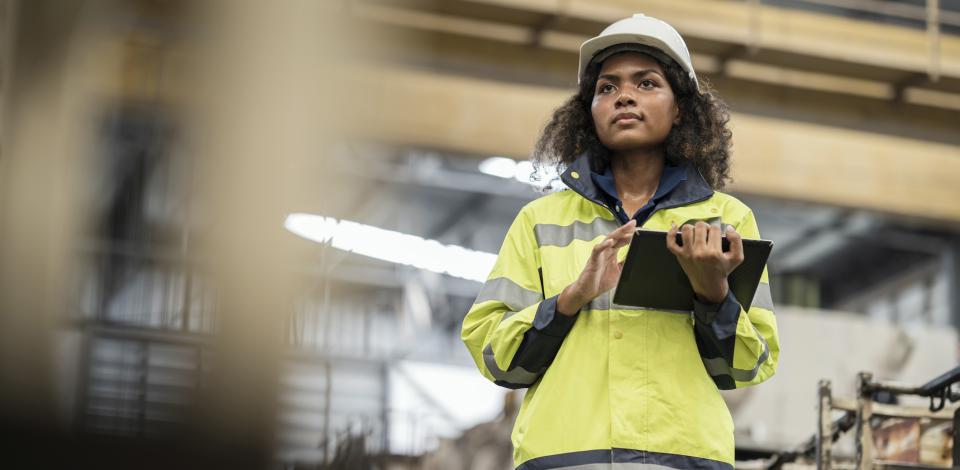
Workplace safety should be a national priority. Many federal and state-based rules and regulations promise to safeguard America's valuable and productive workforce, yet without strict oversight and enforcement, these rules would mean little.
This is where safety managers make their mark. These passionate professionals support workers by championing safer work environments while enforcing strict safety standards and establishing a much-needed culture of safety.
What Does a Safety Manager Do?
Safety managers promote safe and healthy work environments. They accomplish this by inspecting workplaces, pinpointing hazards, and implementing policies or procedures to address any identified safety concerns. Their work could also involve training employees or managers on safe workplace practices while ensuring that workers have the resources and support needed to perform their jobs effectively without putting their health or well-being on the line.
Some safety managers are directly employed by regulatory agencies such as the Occupational Safety and Health Administration (OSHA). However, private-sector employers may also hire safety managers to improve compliance and help manage risks, especially in demanding sectors such as manufacturing or construction.
Important Safety Management Skills
Safety management is a multifaceted practice that draws from many fields of study while integrating extensive regulatory insights. Safety managers must understand the numerous factors that support health and safety in the modern workplace, particularly as they relate to OSHA regulations and other compliance concerns. Critical concepts include:
- Industrial hygiene. Many workplace hazards can lead to illness or injury, but these are often poorly understood— therein proving the need for a purposeful approach to industrial hygiene, guided by knowledgeable safety managers. OSHA clarifies that industrial hygiene involves anticipating, evaluating, and controlling "environmental factors or stresses arising in or from the workplace," especially if these factors are thought to cause sickness or discomfort among workers.
- Hazardous materials management. Certain substances pose a significant threat to human health and safety but may be necessary to carry out critical industrial operations. Hazardous materials management ensures that inherent risks are recognized and dealt with often through strategic ventilation systems, storage methods, and the use of personal protective equipment (PPE). Safety managers should understand which materials qualify as hazardous as well as recognize what it takes to mitigate these concerns.
- Ergonomics. Not all workplace hazards involve dangerous machinery or chemicals. Often, seemingly small or mundane concerns contribute to considerable harm over time. This is where the concept of ergonomics comes into play. OSHA defines it as "fitting a job to a person." This involves purpose-driven processes that address common causes of musculoskeletal disorders (MSDs): lifting heavy items, engaging in repetitive motions, or spending large periods of time in awkward positions. Safety managers should understand how these concerns contribute to injuries and what processes can be implemented to protect workers on a long-term basis.
Soft Skills
Soft skills determine how safety managers interact with workers, executives, and even policymakers. These skills help safety managers communicate potential hazards or gaps in protection while also advocating assertively for necessary changes — and ensuring those changes are enacted. Safety managers are more effective when they actively cultivate soft skills such as:
- Communication. Communication is at the center of effective safety management. No matter what safety managers uncover or how thoroughly they understand the realities of a given workplace, they cannot achieve meaningful change until they properly convey these findings to the necessary stakeholders. This means speaking or writing persuasively, as well as changing communication styles as needed to connect with or spark understanding in various audiences. Effective listening is also essential so that safety managers can fully understand employers' or employees' concerns.
- Emotional intelligence. Interpersonal skills determine not only whether safety managers communicate effectively but also whether their interactions have the intended impact. This begins with understanding various thoughts, perceptions, motives, and behaviors. This understanding forms the basis for rapport and, eventually, genuine trust — which in turn will yield greater buy-in to ensure that all parties take safety managers' insights and recommendations seriously.
- Attention to detail. Safety managers must be detail oriented. Whether examining workplace data or directly observing safety practices within work environments, these professionals should be able to pinpoint discrepancies that others might miss. For example, safety managers might notice slight deviations from safety standards that, if left unchecked, could have devastating consequences.
- Problem-solving. Safety managers encounter new challenges every day. Problem-solving skills allow them to think strategically about these concerns and pursue the best possible course of action based on available information and resources.
Technical Skills
Safety management is increasingly tech-driven, with cutting-edge software and devices promising to streamline and simplify everyday tasks so that safety managers can focus more on connecting with employers or employees. While this field has long been driven by data, the sheer availability of relevant information has increased drastically in response to real-time monitoring systems and other advanced technologies.
At this point, safety managers must make sense of vast quantities of workplace data. This helps confirm whether employers are compliant with all regulations and may also influence risk management strategies or even insurance premiums. Following workplace incidents, root cause analysis helps safety managers identify underlying factors that, if addressed, could prevent similar events from occurring in the future.
Safety managers should feel confident using a variety of risk management techniques to evaluate hazards from both a safety and an economic perspective. Economic analyses help safety managers determine the financial impact of workplace incidents while revealing which safety policies are most capable of yielding a healthy yet productive work environment.
Increasingly, many safety managers use artificial intelligence (AI) and even machine learning to guide this effort; AI solutions can find hidden patterns in workplace information while visualization tools help safety managers convey complex insights to business leaders or even policymakers. These safety manager skills must be underscored by an in-depth understanding of relevant safety regulations and workplace policies.
Becoming a Safety Manager
If you feel drawn to safety management, this career path could allow you to improve the lives of countless workers all while holding employers accountable and instilling a culture of safety in the modern workplace. Success in this unique role calls for targeted preparation. Given the sheer breadth of skills highlighted above, high-level training is crucial for not only finding work in this competitive field but also driving the greatest possible impact.
Education
An essential first step to thriving as a safety manager entails pursuing education in the field. While a bachelor's degree can assist in entry into this field, some individuals may also take courses or earn certificates. For college graduates interested in safety management, a relevant master's program may be of interest.
An excellent option is a Professional Master's in Occupational Safety and Health (PMOSH) like the program offered at Georgia Tech. Designated as a Qualified Academic Program (QAP) by the highly respected Board of Certified Safety Professionals (BCSP), this career-focused curriculum covers key concepts such as industrial hygiene, ergonomics, and risk management.
Another perk of pursuing a PMOSH degree is taking advantage of the Graduate Safety Practitioner (GSP), which offers an alternate pathway to sitting for the Certified Safety Professional (CSP) exam. Available to those who graduate from QAP programs, this credential provides a reliable option for conveying professional credibility.
Training and Job Experience
Master's programs provide a range of opportunities for current and future safety managers to apply core skills and concepts. In addition to these college-driven experiences, it’s worth gaining workplace exposure through entry-level roles or opportunities such as targeted internships or apprenticeships. Hands-on, entry-level experience — combined with further education — can pave the path for an influential career in safety management that allows you to work your way up.
Many successful safety managers get their start as health and safety technicians. This could involve assisting with inspections or otherwise gathering information on workplace health and safety. These technicians may be involved in post-incident investigations too, offering the insights needed for specialists or other higher-level safety management professionals to formulate recommendations for improvement.
Job Outlook
Safety management is a diverse and thriving field featuring various opportunities to make a difference. The U.S. Bureau of Labor Statistics (BLS) highlights a strong outlook of 14% for the role of "occupational health and safety specialists and technicians” between 2023 and 2033. This compares favorably to general workforce projections of a 4% average growth rate across all occupations.
Pursue a Future in Safety Management with Georgia Tech's PMOSH Program
Are you passionate about occupational safety? Georgia Tech’s Professional Master's in Occupational Safety and Health (PMOSH) program can introduce you to critical safety management concepts while empowering you to make a difference in the modern workforce. Request more information about this opportunity today.